We have had a brief run of warm and sunny days. It has been more than a little welcome, even for this rain-lover. Some of my indoor projects have taken a back seat to being out in the yard. I love knitting and spinning outside. And when I have been inside I have been mending a batch of sweaters from a customer. Lots and lots of mending happening here.
Many sweaters pass through my hands. People bring them to Cozy, I take them home for mending, and return them refreshed to their owners. This is not a small thing. Mending is almost always a long and slow process, so I thought I would show you the steps that a knitted item goes through once it is in my mending box.
Mending One Step at a Time
First I do an initial discussion with the sweater’s owner. They show me the holes and damage they know of. I tell them what makes the most sense for each particular garment. Visible or invisible mending? If we are going with visible mending, what colors would they prefer? What should I avoid? Do they have a timeline? I estimate how much it will cost to mend the damage they have showed me.
The sweater is then sealed in a plastic bag. First stop at home is the freezer for about a week. This kills any moths or other critters living in the wool. Even if I am sure that the damage is not caused by moths, it still gets frozen. I let it warm up for 2 days, then freeze it for another two days. The warming allows any live eggs to wake up and a re-freeze takes care of those.
Next is the light board. I have made note of the damage I was told about, but more often than not, there is damage that I didn’t notice in the initial assessment. I run the whole garment over my lightboard, looking for any damage not already identified. In this sweater, I had found 2 holes initially, plus significant wear in the front panel. After I ran it on the light board, I had 6 additional holes to mend. Even if there is only a single snag, I still go over the whole item. It makes no sense to me to mend only a fraction of the issues. Often this extra look means a higher estimate, so before I start mending, I contact the owner with new numbers.
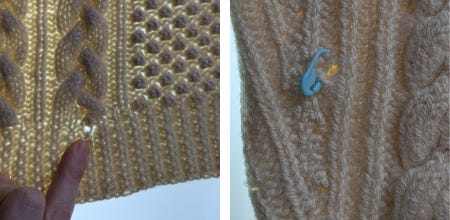
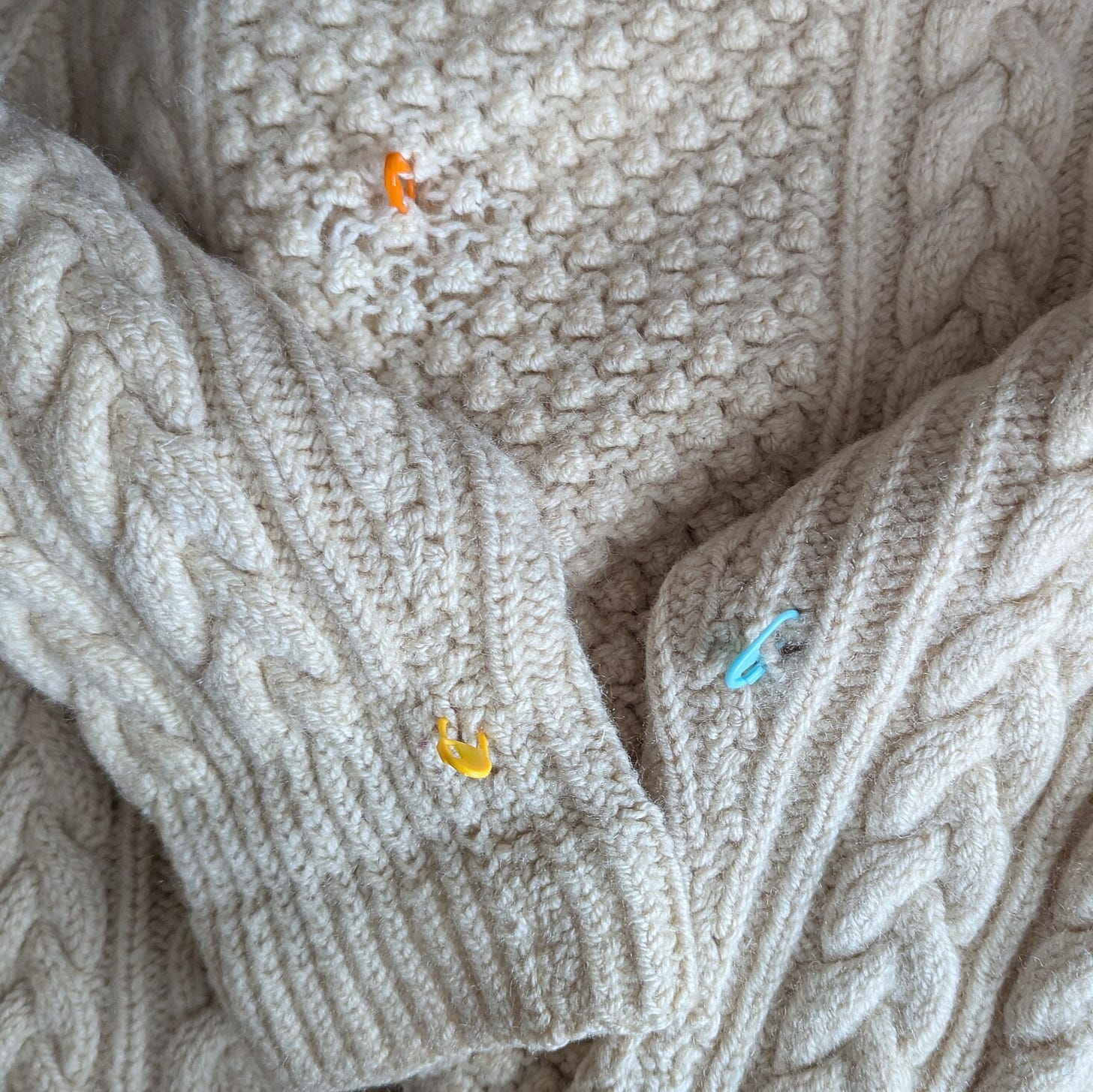
If I am doing an invisible mend, as in this sweater, I have to match the yarn. First I dig through my (not insubstantial) collection of yarn, mending wool, and yarn scraps. If that is unsuccessful, I start hunting to purchase the closest color I can, and asking my fiber community if they have anything that matches. I will need only a few yards to do the mend, but if I have to purchase a whole 200 yard skein, I will.
If I am doing a visible mend, I gather my colors and start to play with design. I send a sample image to the owner for their approval before I really get going. At this point I haven’t even started the mending, and I have probably spent at least a half hour just on assessment and preparation.
There is no good way to mechanize the mending of knitwear. The pull of any sewing machine or knitting machine will distort the existing fabric and the mend will be lumpy and strange. Each area of mending must be filled stitch by stitch by hand, taking care that the mend works with the fabric around it.
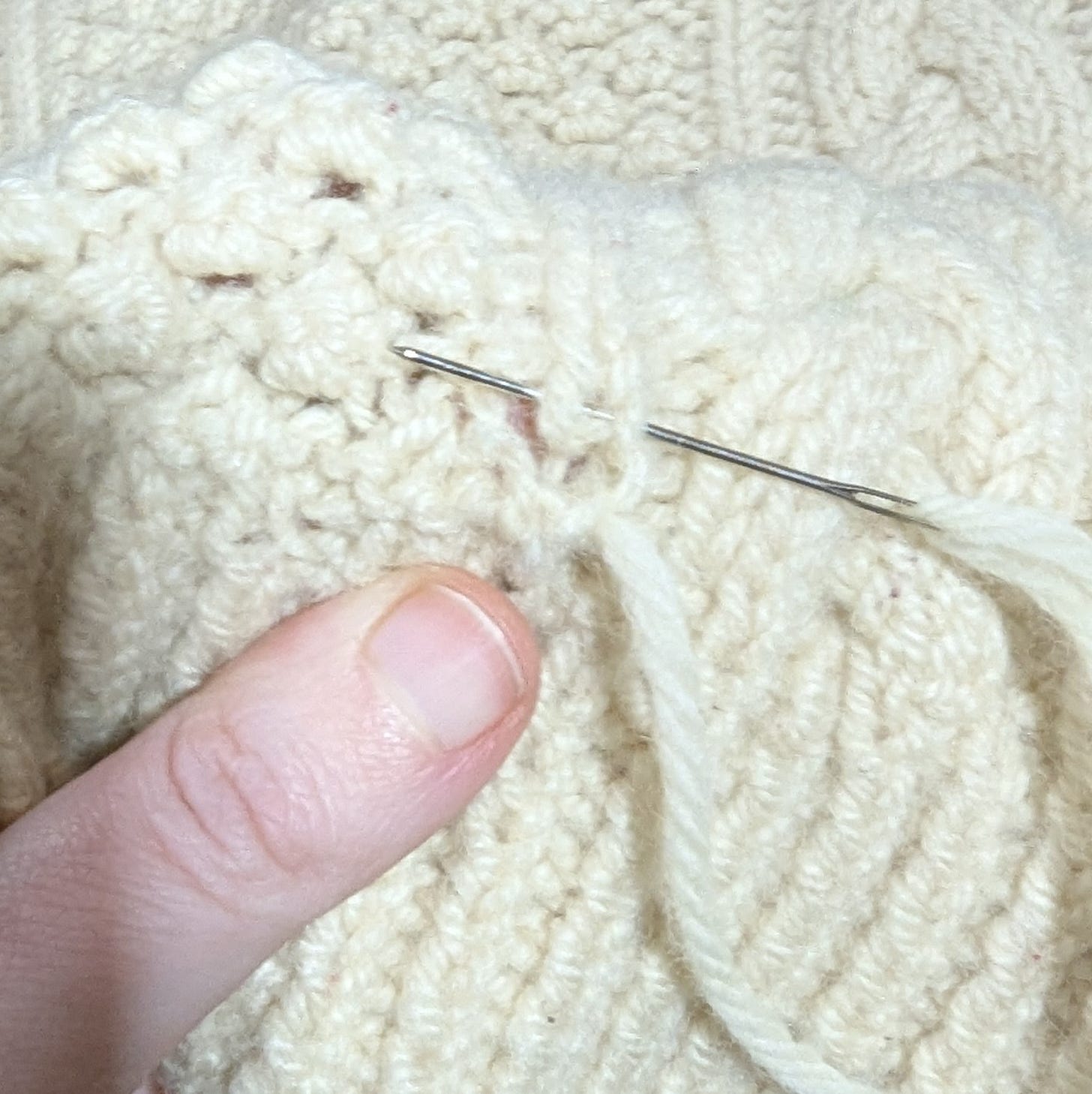
At long last, the mending begins. Each hole is carefully filled, trying my best to mimic the existing fabric with the best darning method for the hole in question. In the case of this Aran sweater, most of the holes could be filled with Swiss darning that is almost entirely unnoticeable at first (and second) glance. The fraying ribbing at the bottom was stabilized with a blanket stitch, and the wear on the front was filled in. Eight holes, ribbing, and the front fill took about 1.5 hours.
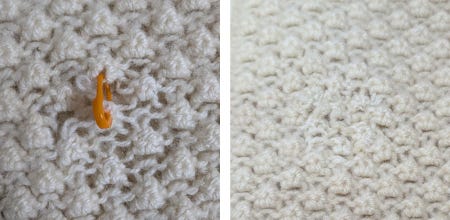
But we aren’t done yet! The next step is a bath in Eucalan. There are two reasons for this. The first is simply that I want to give a clean, renewed sweater back to it’s owner. The second is that when the wool absorbs water, weak spots that are about to break will break. They might have looked fine on the light board, but a good soak can prove otherwise. I would rather have new holes to mend than have the sweater back again in a couple of months. My goal is always to give back a sweater that has had its life substantially lengthened.

New holes are marked and the sweater is left to dry flat for 1-3 days, depending on the weight of the sweater. This is the trickiest part because I do not have a guest bed or other large, flat surface for drying a sweater. Often they move around, from one surface to another - on my bed during the day, on the couch while everyone is in their beds - until they are dry.
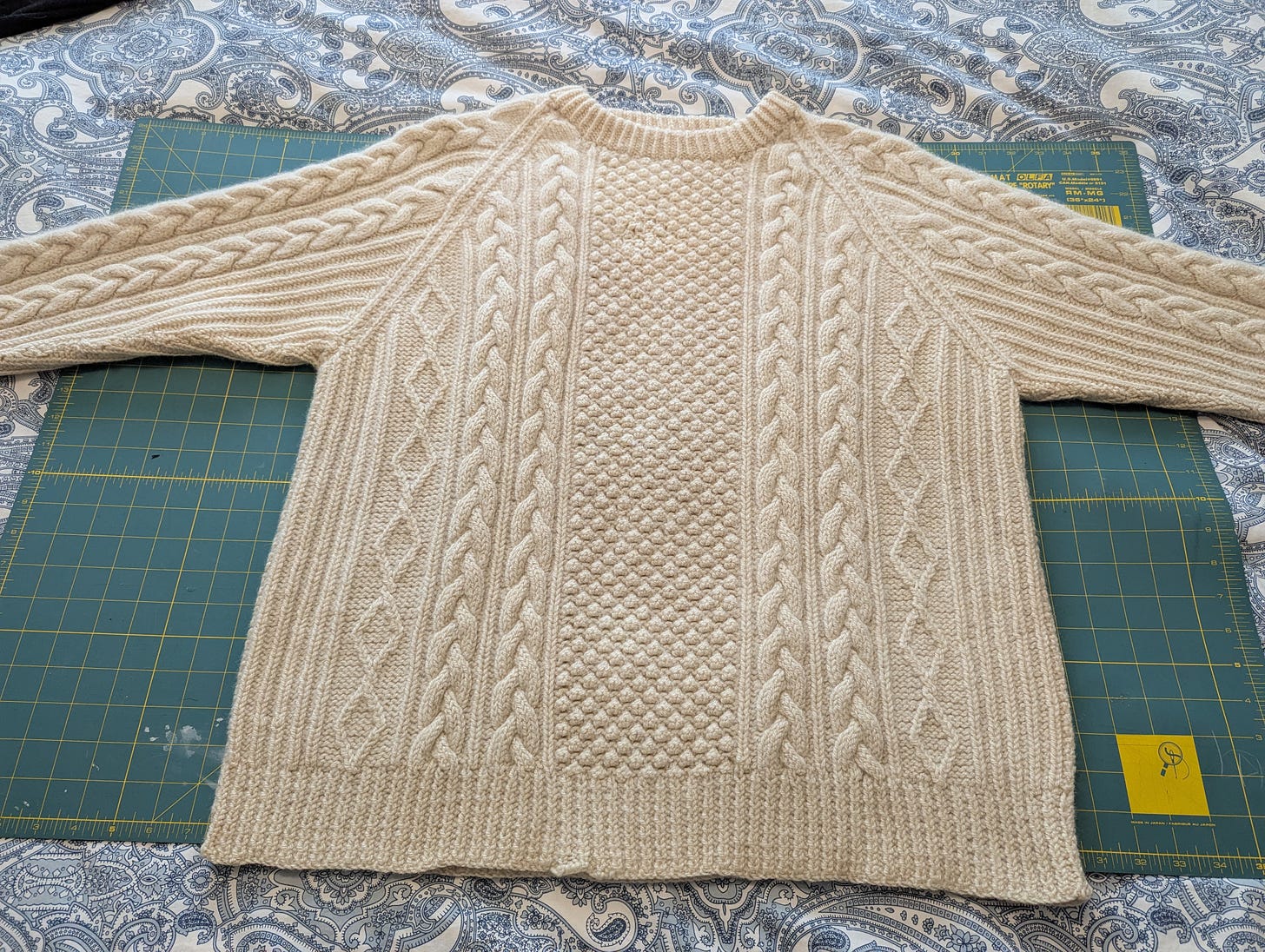
Finally, I mend any new holes and give the whole sweater a once over with my sweater shaver, removing any pills. This gives me one more chance to find any sneaky holes. The sweater is folded, an invoice is written, and it is ready to be returned to the owner. The whole process can take from a single hour, to as much as 3 or 4 hours (not counting the time freezing, soaking, and drying), depending on the sweater and the damage found.
Octopus Update
I have added some octopus media to my days, to make this fun knitting project even more interesting. I knit about half an arm while watching My Octopus Teacher. Next up I am going to read Remarkably Bright Creatures by Shelby Van Pelt - probably as an audio book so I can knit and read at the same time.
I am happy to report that we have two octopus arms! They aren’t as much knitting as I worried they might be, and they go fairly quickly. The wrapped stitch I added to the underarm are slightly annoying, but they add a pleasing texture that suggests suckers.
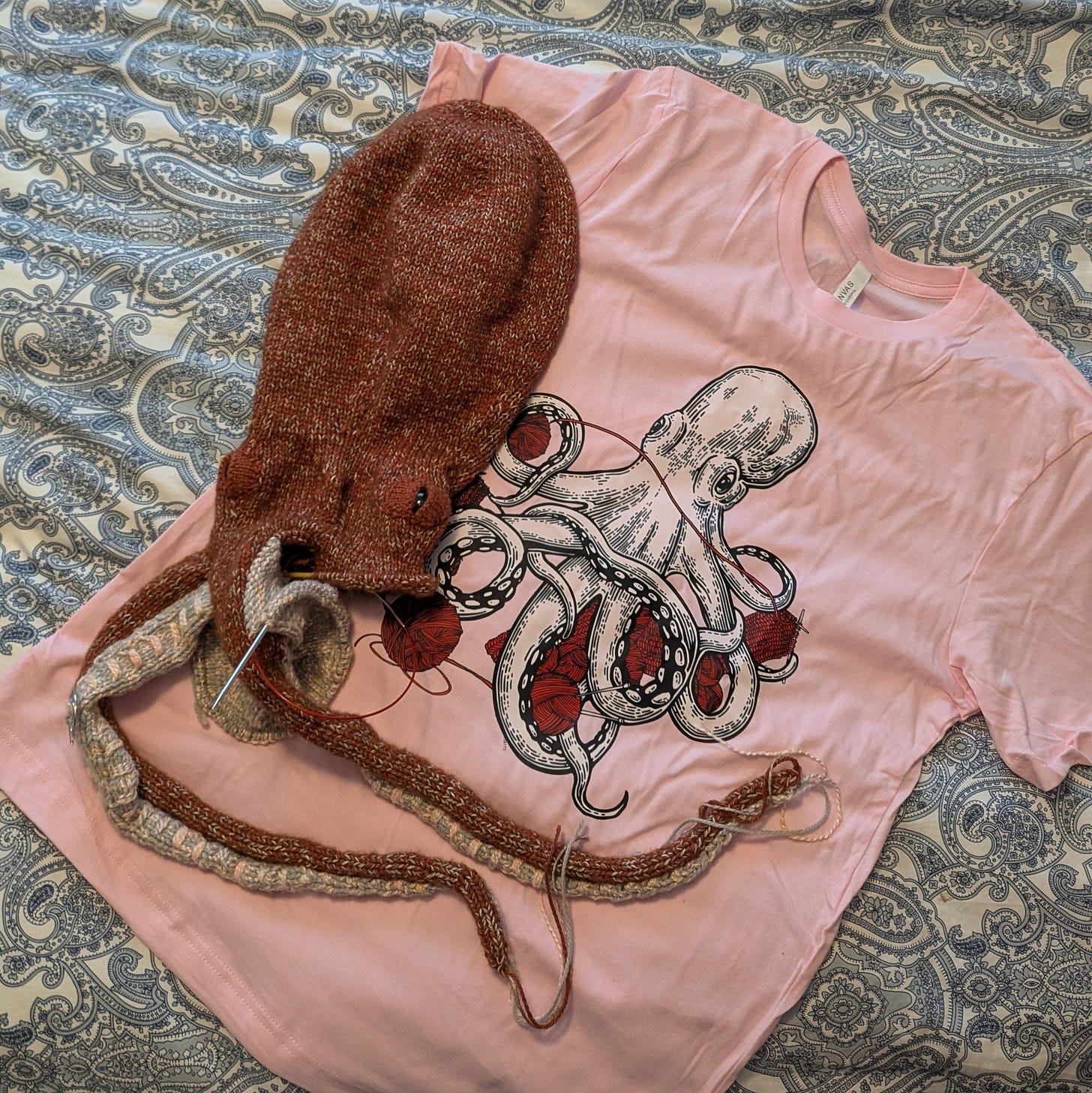
Knit for Food
Coming up is a Knit-A-Thon! It is similar to a jog-a-thon, but much more my speed. I commit to a full day of knitting on April 5th with my local fiber group, Yarnies541. Folks donate money to our team. After the Knit-A-Thon, the raised funds are divided between Meals on Wheels, Feeding America, World Central Kitchen, and No Kid Hungry. Last year our team raised more than $500, and all the teams combined raised approximately $379,000. You can learn more about the Knit-a-Thon here.
Last year I knit my 100th Gnome from the wonderful patterns by Sarah Schira. And he wasn’t just any Gnome. I contrived to knit him in a bottle. I haven’t come up with anything that exciting this year, but I’ve still got some time to think on it.

Please consider donating to this very worthy cause. This link will get you to my team’s donation page. With the fragility of funding for anything federal, organized fundraisers such as this are more important than ever. If you are interested in joining us as we knit, crochet, spin, or otherwise craft, leave a comment or send me a message and I will send you our plan for the day.
Thank you for DONATING!
I think that is all for now. My mending box is calling me. There are some elbow patches to stitch and buttons to put on my husband’s shirt. And if I can get some of those jobs done, I may have more time to get out in my garden.
I hope you find something small to bring a smile to your face today.
LOve you Tay....Did I mention Octavia as a name for your knitted Octopus project!? I too love mending , in all arenas...you are a Champion tho-Thank you for your good works-xo Ali K.